ウツミの強み
- ホーム
- ウツミの強み
ようこそ、内海機械のショールームへ
5S(整理・整頓・清掃・清潔・しつけ)や3定(定品、定位置、定量)、見える化に取り組み、見て感動する工場を実現。
様々な小さな改善の積み重ねを行い、生産性を3割向上することができました。
015S
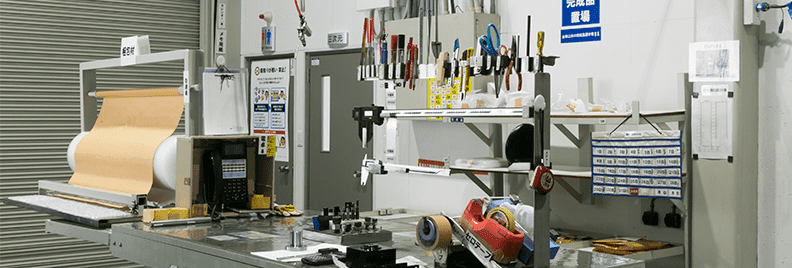
「5Sで1番」を目指す
単品加工・超短納期を実現するためには、現場環境や製造過程の徹底的な改革が必要でした。「地域のお手本になる、感動を呼ぶ工場へ」を最終目標に、まず製造業における職場環境改善の定石、「5S」:「整理」「整頓」「清掃」「清潔」「しつけ」の徹底に着手。まずは社員へのビジョンの共有からスタートし、「5Sで一番」を掲げて全社員一丸となって現場の大改造に乗り出しました。
会社全員で行った断捨離作業で廃棄された総量は、なんと9t。それまで雑然と整理されていた数千という工具・用具は、ひと目でわかるように大きさ・用途別・使用頻度別にカテゴライズされ、ひとつひとつラベリング・ナンバリング。飛び散って床を汚しがちな切粉は、カバーで飛散を防止しリサイクルできるように。キャビネットはゆるやかに角度をつけ、開閉に時間を取らないように。壁やそれまでのデッドスペースは次々と収納として生まれ変わり、混在しそうな小さなもの・細かいものものには、社員がアイデアと技術を生かし、工夫をこらしたさまざまな専用収納を制作。あらゆるものの置き場を明確にし、隅から隅までくまなく「見える」化を実践しました。
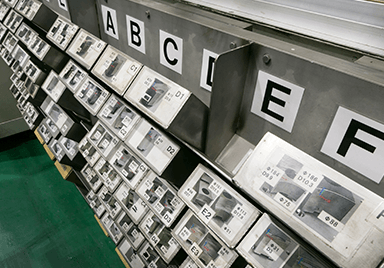

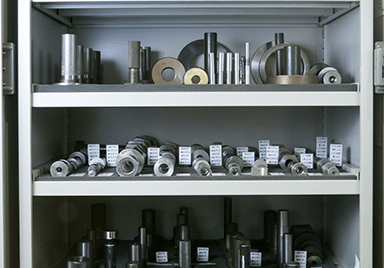
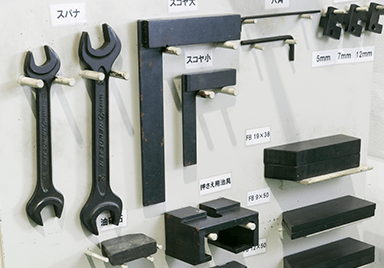
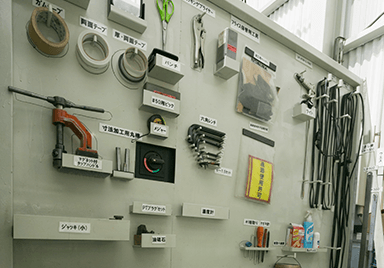
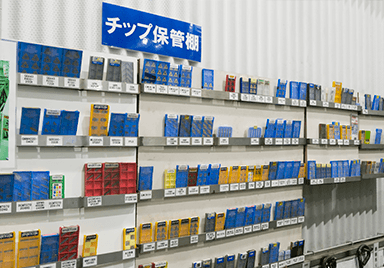
02魅せる工場
「見える」から「見せる」
そして「魅せる」へ
徹底的な整理整頓とからくり改善、作業効率を最大限に引き出す配置によって「見える」化された現場ですが、「感動を呼ぶ」ためにはさらに「見せる」そして「魅せる」工場でなくてはいけません。内海機械では、作業中の工具の放置や「もしかしたら使うかも」の無駄が無いよう前準備から段取り・片付けにいたるまで「定位」「定品」「定量」の3定と呼ばれる整理の基本ルールを社員に徹底教育。作業エリアの相互チェックや、5Sについての個々の目標計画に至るまでしくみ化・共有することで「見せる」を常態へと定着させ、現在では日本各地から見学者が訪れる「魅せる」工場として、書籍に取り上げられるまでになっています。
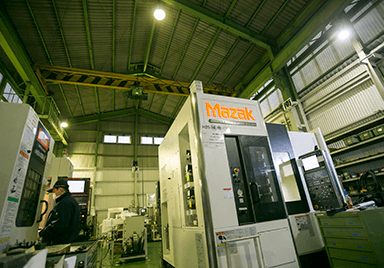
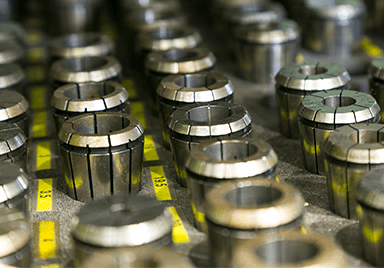
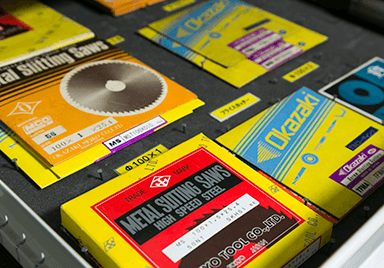
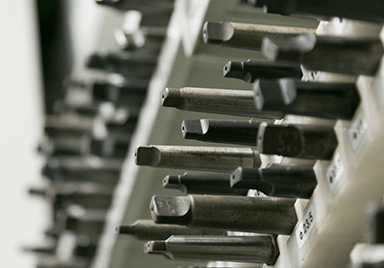
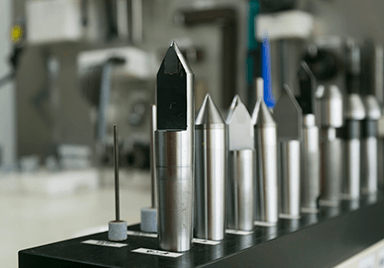
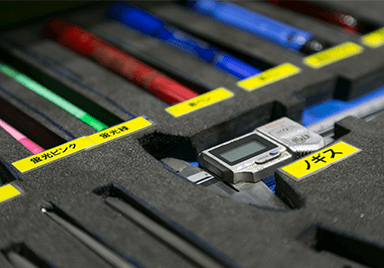
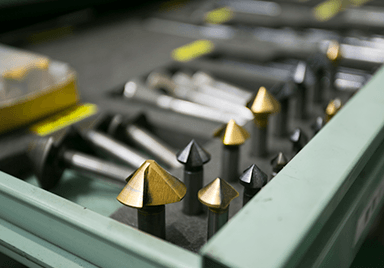
0316大ロス
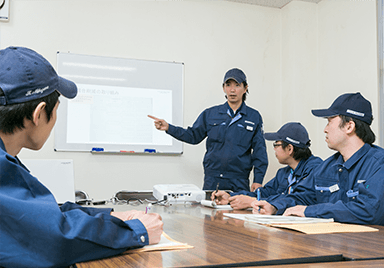
16大ロスの徹底削減
生産効率を極限まで高め、超最短納期を実現するためには、「生産活動における16大ロス」も極限まで削減することが必要です。例えば、不具合手直しロスの改善のために現象から追求していく「原因遡及分析」では、根本原因まで深く掘り下げその対策まで詳細に分析。また、段取りや調整でのロスゼロを目指し、写真などを配した手順書の設置や人の動作ロスをおさえるための社員への前準備教育を徹底し、トイレの使用状況がわかるランプまで配置。「見える化」と「共有」をキーワードに全方位からロス削減を行い、極限まで作業を効率化しています。
04スマート・ファクトリー
世界標準のスマート・ファクトリーを目指して
ドイツ政府が推進し、世界のものづくりの現場をIOTで変えた革新的プロジェクト「インダストリー4.0」。そこで提唱された「スマート・ファクトリー」とは、工場内の機械や設備をインターネットでつなげ収集されたデータを分析・活用することで、最大のパフォーマンスを導き出された工場を意味します。内海機械では、超短納期を実現するために最新の設備を導入し、世界標準の「スマートファクトリー」を目指し機器の稼働状況をIOTで「見える化」。全ての機械を扱える多能工にとって、最短で最大のパフォーマンスをひと目で可能にしています。
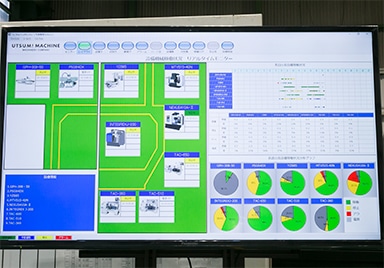
05マルチな多能工
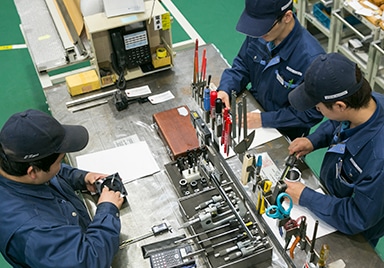
常に上を目指して
マルチな多能工がやりがいを持って働く現場へ
内海機械の社員は、二度と同じものを作ることはありません。受注のたびに新しい図面を受け取り、作業工程から使用する機械まで全てのソフトとハードを使いこなして超短納期を実現できるのは、彼らが自己研鑽を怠らない優秀な多能工だからこそ。4年生大学を卒業した新入社員たちは、厳しい新人教育に加え1年で10以上の実務資格を取得。すべての分野において卓越した知識と技術を身につけます。さらに研修を重ねた社員たちは、製品やサービスの価値の向上を専門的な知識でプラニングする「VE(Value Engineering)リーダー」の難関資格も取得しています。
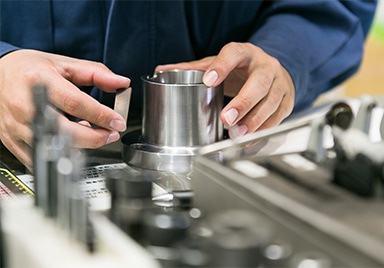
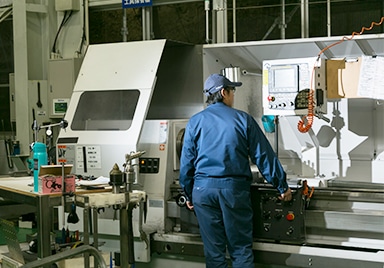
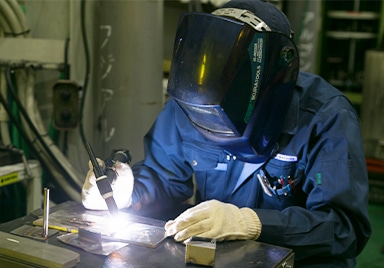
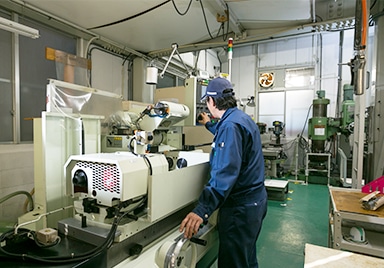
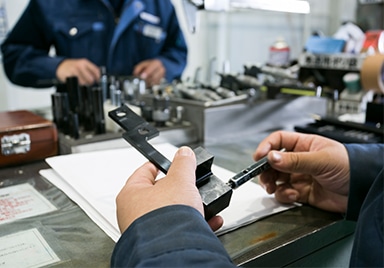
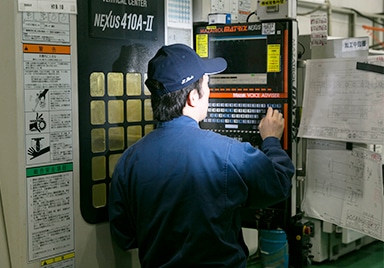
取得資格一覧
取得資格名 |
|
---|